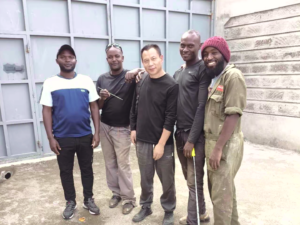
Kiln Drying Brings Stabilized Moisture 8–12% and Unmatched Efficiency Our Client a leading furniture manufacturer from Kenya, bought tech drying kilns to solve long struggled tropical timber drying issues. Moisture deviation caused 25% EU order rejections and 15% hardwood cracking, while natural drying and slow kiln drying failed to meet 45-day deadlines, limiting peak-season growth. […]
This post Kiln Drying Unlocks Kenya’s Furniture Export Success: Conquer Moisture, Boost Profits first appeared on TECH Drying Kiln and is written by shujin9213@gmail.com
]]>This post Kiln Drying Unlocks Kenya’s Furniture Export Success: Conquer Moisture, Boost Profits first appeared on TECH Drying Kiln and is written by shujin9213@gmail.com
]]>6 Repurchases: Kiln Dryers Power Gabon Africa’s Timber Excellence Rimbunan Hijau Group Made 6 Repurchases of our Kiln Dryers in Gabon, Africa Since 2007, the
This post 6 Repurchases: Kiln Dryers Power Gabon Africa’s Timber Excellence first appeared on TECH Drying Kiln and is written by shujin9213@gmail.com
]]>This post 6 Repurchases: Kiln Dryers Power Gabon Africa’s Timber Excellence first appeared on TECH Drying Kiln and is written by shujin9213@gmail.com
]]>How TECH Dry Kilns Conquered the Russian Climate for a Wood Company TECH Dry Kilns for a Russian Wood Company A leading Russian wood company
This post How Our Kilns Conquered the Russian Climate first appeared on TECH Drying Kiln and is written by shujin9213@gmail.com
]]>This post How Our Kilns Conquered the Russian Climate first appeared on TECH Drying Kiln and is written by shujin9213@gmail.com
]]>Purchased 112 Drying Kilns at once 112 Drying Kilns Purchased at once by our Mahogany Furniture Client Niannianhong Group?? has trusted our drying solutions since
This post 112 Kilns at Once for Furniture Company first appeared on TECH Drying Kiln and is written by shujin9213@gmail.com
]]>This post 112 Kilns at Once for Furniture Company first appeared on TECH Drying Kiln and is written by shujin9213@gmail.com
]]>Clients Love Our Wood Dryers After bringing in 32 wood dryers from Tech Drying Co., the wood processing procedures in Bangladeshi client company have changed
This post 32 Wood Dryers Transform Bangladesh Timber into Asset first appeared on TECH Drying Kiln and is written by shujin9213@gmail.com
]]>This post 32 Wood Dryers Transform Bangladesh Timber into Asset first appeared on TECH Drying Kiln and is written by shujin9213@gmail.com
]]>Unleashing the Potential of Floor Carbonization: TECH Thermal Modification Kilns Jiusheng Flooring’s 16 TECH Kilns and Challenge – Beating Strategies Jiusheng Flooring Co., Ltd., a
This post Floor Carbonization: 16 Thermal Modification Kilns first appeared on TECH Drying Kiln and is written by shujin9213@gmail.com
]]>This post Floor Carbonization: 16 Thermal Modification Kilns first appeared on TECH Drying Kiln and is written by shujin9213@gmail.com
]]>Table of Contents Furniture Company in Brazil transformed its radiata pine drying process by purchasing our high-speed softwood drying kilns. This innovative fast drying technology
This post Drying Kiln for Radiata Pine: A Success Story from ?Brazil first appeared on TECH Drying Kiln and is written by shujin9213@gmail.com
]]>This post Drying Kiln for Radiata Pine: A Success Story from ?Brazil first appeared on TECH Drying Kiln and is written by shujin9213@gmail.com
]]>